BuildTop (Prototype)
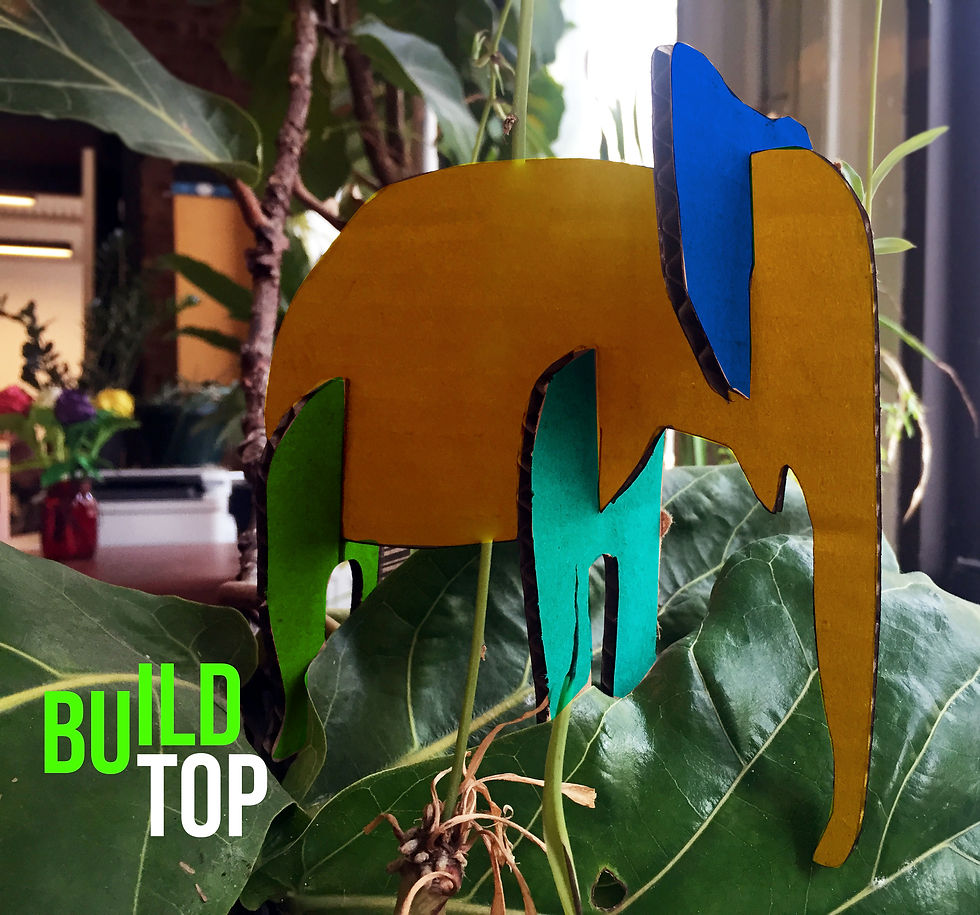
Recently in Singapore, there has been a spike in number of children with a minimum age of 8 years old seeking help for mental issues. While some of this mental issues are not related to hereditary illnesses, they may be the cause of extreme stress living in Singapore. Anxiety, depression, self-harming, social withdrawal are some of the behaviours that have recently been accounted for.
Experts believe that the rise in the number of stressed-out children and youth in Singapore could be caused by the demands of school, however, the stress often stems from multiple sources.
Some of the children have trouble making friends or being accepted by their peers, face family problems or have high personal expectations.
Looking into the matter, I thought of a simple and inexpensive way to create a tangible interaction between the children and increase their social presence/awareness. Inspired by the current trend of today's technology, I wanted to create an object where they could fix themselves and at the same time, interchange between one another to create a far more interesting object. Just imagine transformers, lego and MindCraft equipped with VR capabilities using the everyday smart phone.
BuildTop (prototype) is made out of cardboard, it is an inexpensive alternative for the price conscious. The idea of the toy is for the children to be able to fix each parts and create an object/animal of their own. While there are some direct templates for them to follow, the structure of the toy is flexible enough for children to mix and match.
Inspiration: edo do everything
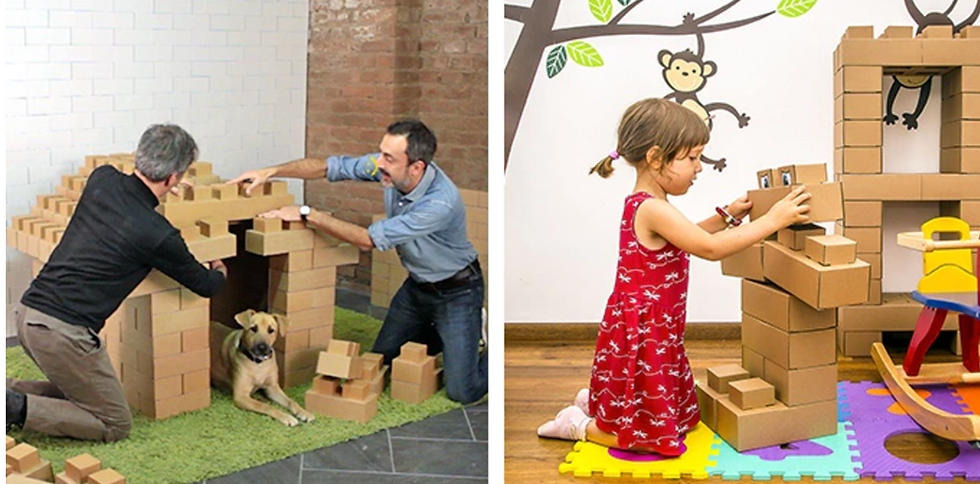
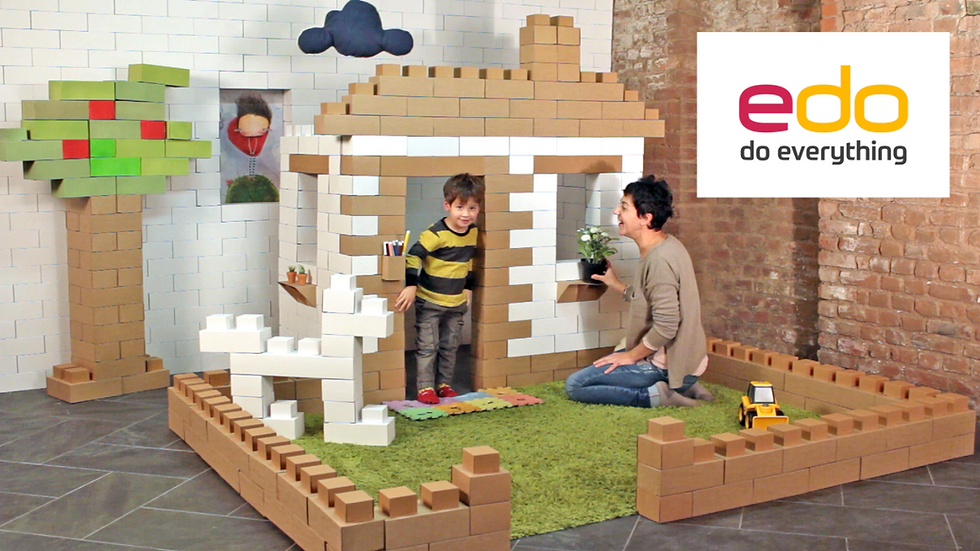
I was inspired by the company edo do everything , however the concept of the company was more to life-size lego like. I wanted something miniature that these children could bring around anywhere.
I sketched out my intended animal, in this case, I wanted it to be an elephant.

I transfered the image to illustrator where I refined the drawing as well as the measurement for the joint.
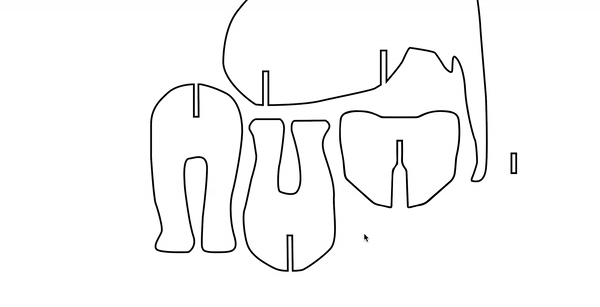

The process to create the pieces was not an easy task. I created about 10 pieces of vector laser cutting before arriving to proper setting that would cut the piece of cardboard I was using. The settings that was made for cardboard did not really work for me. I was resorted to using 100F, 30s and full power.


I was however happy with the results. This project could be carried forward in the future to implement VR capabilties, much like the pokemon Go.